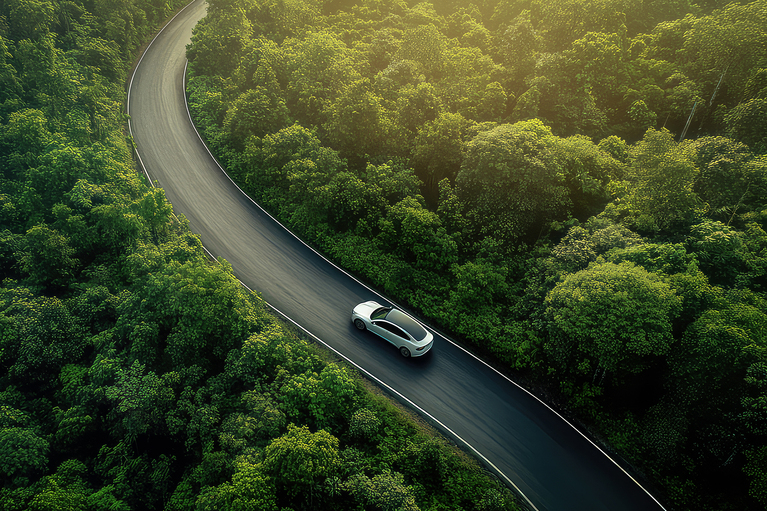
Active suspension systems in electric vehicles
48V power systems reduce losses and downsize power designs. Vicor is making the transition from 12V to 48V easier, delivering a competitive advantage
Leveraging an EV’s high voltage battery to deliver 12V more efficiently.
By Nicolas Richard, Director Automotive Business Development, Vicor Europe
Yes, the 12V lead-acid car battery is dead. Europe has decreed that no new cars will have lead-acid batteries after 2030, creating a considerable challenge for OEMs to find alternative solutions. While this may seem like a daunting task, it also presents a tremendous opportunity to eliminate the environmentally toxic battery while also reducing weight in a vehicle and improving overall efficiency.
The 12V battery and power delivery network (PDN) are standard across the globe, supporting hundreds of loads, including some critically related to safety, so the solution will need to be both innovative and robust. High-density, high-power and efficient power modules used to interconnect high-voltage, 48V and 12V PDNs offer the most flexible and scalable solution to this impending challenge.
When considering potential solutions, OEMs must take into account a number of key factors: adding more power to support new features with better performance, increasing efficiency for longer range and better thermal management, reducing CO2, optimizing cable routing, reducing harness weight and meeting EMI requirements are some of the variables within this complex equation.
There are two primary options for solving this equation. Replacing the 12V lead-acid battery with a 12V Li-ion battery is one option. While it does slightly reduce weight, it retains the decades-old legacy of the 12V PDN, which yields no additional benefits. The other option is to support a 12V PDN powered from the primary 400V or 800V battery in EV and HEV/PHEV. There are many benefits to the latter option, but both merit further exploration.
Simply replacing the 12V lead-acid battery with a 12V Li-ion battery saves ~55% weight; however, it has a high cost impact. The 12V Li-ion battery needs a Battery Management System (BMS) to control the charging and maintain the full battery operation over the vehicle life. It is the direction taken for instance by Tesla and Hyundai .
Furthermore, adding a bulky DC-DC converter from HV to 12V (with voltage and current regulation feature) is needed to recharge the 12V Li-Ion battery and supply the electrical loads. But this adds no benefits. What it does add is weight, vehicle packaging complexity, and system cost; it also reduces overall vehicle reliability. By contrast, eliminating the 12V battery altogether removes 13kg from the vehicle and can improve the cargo space by 2.4%.
Maintaining a physical 12V battery means maintaining an inefficient PDN with unnecessary redundancy. In a typical automotive 12V PDN, all the 12V loads connected to the 12V bus have internal pre-regulators able to convert wide input voltage range typically from 6 to 16V to regulated rails of 5V, 3.3V or lower. From a global system view for an EV, HEV or PHEV, there is redundancy of series regulator stages. A high-voltage-to-12V DC-DC converter regulates the 12V bus (with efficiency hit) and the pre-regulator provides the suitable internal rail voltage for each load (Figure 1).
This legacy architecture originated when vehicles had an alternator, a sensitive 12V PDN that needed regulation to charge the battery, keep the radio operating during cranking event or maintain incandescent headlights at the right intensity. OEMs were very creative to bypass the 12V power limitation and complex electrical architectures have been designed in recent years with two 12V batteries, one 24V battery for power steering and several DC-DC converters between them.
Figure 1: Typical E/E used in xEVs with 12V battery using redundant voltage regulator stages. The HV-to-12V DC-DC regulates the 12V output to charge the 12V battery. Every 12V load in the vehicles has a pre-regulator stage to supply the proper rail voltage needed for the load to operate.
A better approach to solving this problem is to completely rethink the PDN in a vehicle: eliminate the physical 12V battery and replace it with a 12V “virtual” battery from the primary EV battery (Figure 2). Every EV carries a main battery, so it does not make sense to transport additional energy storage devices. The ideal vehicle architecture would be one high-voltage (HV) battery used to power the powertrain and all the auxiliary loads. Vicor high-density bus converter module technology enables this approach by virtualizing a low-voltage battery (48 or 12V) directly from the HV battery (400 or 800V).
Figure 2: Optimized E/E architecture eliminates the physical 12V battery. A virtual 12V battery is created by transforming the high-voltage battery with Vicor BCM Bus Converter technology.
Utilizing zero-voltage, zero-current switching (ZVS/ZCS), Vicor BCM® Bus Converters operate at higher frequencies than conventional converters making them more responsive than a physical battery. For example, the BCM6135 operates at 1.2MHz and, unlike a conventional ZVS/ZCS resonant converter, the BCM operates within a narrow band frequency (Figure 3). The BCM’s high-frequency operation provides a fast response to changes in load currents and a low-impedance path from input to output. Fixed-ratio conversion, bidirectional operation, fast transient response (higher than 8megaamps per second), and a low-impedance path collectively enable the BCM to make HV battery appear like a 48V battery, which we term “transformation.” This ability to transform a power source is both the key benefit and key differentiator when compared to conventional converters.
Figure 3: The fast load transient response of BCM6135 is the key to supporting the 12V loads. The transient response is 8 MA/s or 8 million Amperes per second. Yellow : input voltage (800VDC), Red: output voltage (48V), Blue: output current.
Figure 4: Functional block diagram of BCM Bus Converter. Even though it converts DC to DC, the BCM uses a transformer to convert AC to AC at high efficiency, scaling the magnitude by the K factor and using the switching blocks to convert between AC and DC. The switching is done at a high frequency, and, due to the transformer-like energy transfer the conversion, has a fast response to transient load changes and presents a low-impedance path between input and output.
The Vicor BCM operates as a fixed-ratio converter where the output voltage is a fixed fraction of the input voltage. The Vicor BCM6135 converter is isolated and provides 2.5kW of power in a 61 x 35 x 7mm package with over 97% peak efficiency. It can be paralleled easily in an array to deliver even more power.
The fixed-ratio nature of the BCM ensures that the virtual battery will stay within its appropriate operating range. For example, the HV battery is guaranteed to stay between 520 and 920V on an 800V battery-powered electric vehicle. A BCM6135 with 1/16 ratio virtualizes a 48V battery with a voltage range guaranteed to stay between 32.5 and 57.5V. A BCM6135 1/8 ratio could be used for 400V EVs (Figure 3).
The battery virtualization can also be extended to the 12V bus with a fixed-ratio converter of 1/4. In that case, galvanic isolation is not required and a Vicor NBM™ Bus Converter could be used. Identical in all other features to a BCM, the NBM non-isolated bus converter has all the same benefits previously described: fast transient response, low impedance, and bidirectional operation. The voltage range on the 12V stays between 8.125 and 14.375V with a fixed ratio to the HV battery voltage. BCM and NBM technology are ideal transformers connecting each of the vehicle power networks.
Table 1: Minimum and maximum voltages on the 48V bus and 12V bus with Vicor BCM/NBM bus converter technology. Both 48V and 12V voltage ranges are VDA 320 and LV 124 compliant.
Figure 5: E/E architecture with 12V and 48V battery virtualization based on BCM6135 and NBM2317 modules. The 48V bus also serves as a more efficient source for powering higher loads in a vehicle such as the A/C condenser, water pump and active chassis stabilization systems.
Ensuring redundancy of power delivery for functional safety loads is essential. Because Vicor power modules are fully scalable in power and delivery, they can be designed to act as redundant PDNs enabling functionally safety-critical loads to be supplied with two dedicated power conversion paths. Ultimately, OEMs could implement localized energy storage to ensure functionally safe operating of critical systems such as ADAS, steering and braking.
The 12-volt lead-acid battery will soon meet its demise in Europe. And the timing is perfect given all the innovation that is driving the redesign of the EV power delivery network.
The automotive electrical PDN is at a crossroads with 12V power delivery. More and more demanding power loads are being implemented in vehicles while trying to keep architectural changes to a minimum. “What are we still doing at twelve volts? Twelve volts is very much a vestigial voltage, it’s certainly low,” said Elon Musk, Tesla CEO.
OEMs are scrambling to design better PDNs to deliver more EV range and performance. Eliminating the 12V battery altogether is the obvious long-term solution that reduces weight and space and delivers better transient response and system performance. Vicor technology not only enables these benefits but also offers an unequaled combination of flexibility, scalability and power density. The Vicor module approach to PDNs offers the ideal building blocks to address the near-term challenge of 12V power delivery network for next generation of xEVs.
This article was originally published by Power Electronic Europe.
Prior joining Vicor, Nicolas worked at IDT (Renesas) as the North America Automotive Segment leader focused on technical sales in powertrain, infotainment and ADAS based systems. Prior to IDT, he spent four years at ON Semiconductor in the role of Field Application Engineer leading an internal design and applications team as a “Concept to Product Champion” heading up the company’s new product growth strategy for automotive sales in Detroit, MI. His background also includes nine years of engineering and development at Continental Automotive where he held various engineering roles in their hybrid and electric vehicle divisions designing DC-DC converters and traction inverters.
Nicolas Richard, Director Automotive Business Development, Vicor Europe
Active suspension systems in electric vehicles
48V power systems reduce losses and downsize power designs. Vicor is making the transition from 12V to 48V easier, delivering a competitive advantage
Power modules accelerate the path from 800V to 48V SELV in automotive
Vicor BCM6135 solves historic power design problems for active suspension. Bidirectional and fast-transient DC-DC converters are essential to new design
High-voltage bus converter power modules for electric vehicle 48V power delivery networks
48V architectures reduce losses and can facilitate smaller, lighter power systems. Vicor DC-DC converters optimize power systems beyond discrete designs
Vicor presented converting high voltage to SELV at AID 2025
Soft switching topology and higher switching frequencies reduce package weight and size when converting HV to SELV. Learn more about Vicor power modules