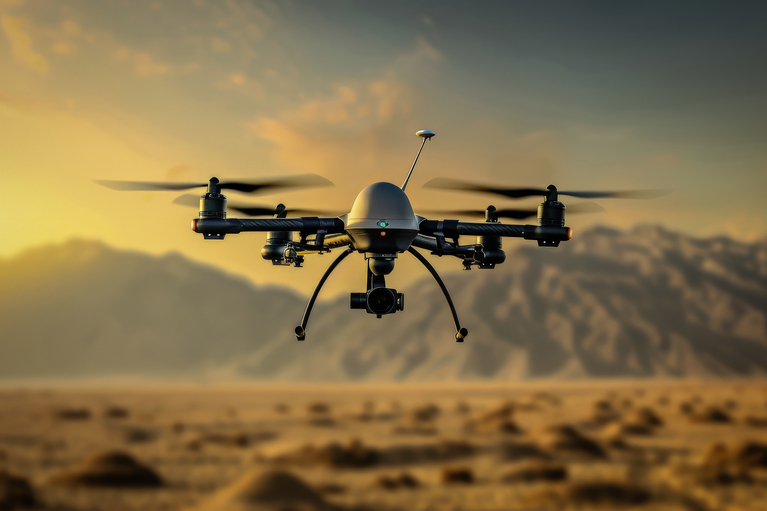
Build better UAVs using modular power
Power Delivery Networks (PDN) based on Vicor high performance power modules enable innovative designs for the next generation of UAV development
Fixed-ratio converters are often the best way of minimizing the electrical current sent over significant distances in the interest of better power efficiency.
By Phil Davies, Corporate Vice President, Global Sales and Marketing
The vast majority of electromechanical or semiconductor loads require stable DC-DC voltage conversion and tight regulation to operate reliably. The DC-DC converters that perform this function are commonly called point-of-load (PoL) regulators and are designed with a maximum and minimum input voltage specification defining their stable operating range. The power delivery network (PDN) to these regulators can vary in complexity based on the number and type of loads, overall system architecture, load power levels, voltage levels (conversion stages), as well as isolation and regulation requirements.
Many power system designers consider regulated DC-DC converters as essential to their overall systems design. However, PDN regulation is not always necessary for providing the right level of voltage to the PoL regulators nor imperative to an intermediate distribution-bus voltage. With this in mind, power system engineers should consider implementing fixed-ratio DC-DC converters, which can offer significant advantages to the overall performance of the PDN.
PDN performance is commonly measured in terms of power loss, transient response, physical size, weight and cost. One major design challenge impacting PDN performance is the number of times the network needs voltage conversion and tight line/load regulation. Engineers spend a great deal of time optimizing bulk power voltage conversion, dynamic regulation and distribution qualities to deliver high performance and reliability.
If system load power is in the multi-kilowatt range, designing the bulk PDN to handle a high voltage reduces the current the system must distribute (P= V×I). Consequently, the PDN size, weight, and cost (cables, bus bars, motherboard copper power planes) can be reduced (PLOSS = I2R). Thus designers strive to keep as much circuitry as possible operating at high-voltage/low-current, only converting to low-voltage/high-current close to the load.
However, bringing a high-voltage and high-power PDN close to the load requires a DC‑DC converter with high efficiency and high power density. If the circuit demands a large step-down in voltage, as from 800 or 400V to 48V, the converters able to do the job and having the highest efficiency would be fixed-ratio converters. These converters provide no regulation and dissipate little power. Their high efficiency figure-of-merit enables higher power density and easier thermal management.
Figure 1: A bidirectional fixed-ratio converter operating as a step-down converter with K = 1/16 can also serve as a boost converter with a K of 16/1.
A fixed-ratio converter operates much like a transformer but instead of AC-AC conversion, performs DC-DC conversion with the output voltage being a fixed fraction of the DC input voltage. As with a transformer, the converter provides no output voltage regulation, and the input-to-output voltage transformation is defined by the “turns ratio” of the device. This turns ratio, referred to as the K factor, is expressed as a fraction relative to its voltage step-down capability. K factors can range from a K = 1 to as low as K = 1/72 and are selected based on PDN architecture and the PoL regulator design specifications. Typical PDN voltages are categorized as low voltage (LV), high voltage (HV) and to ultra-high voltage (UHV).
Fixed-ratio converters can be isolated or non-isolated and also capable of bidirectional power flow with reverse voltage conversion. For example, a K = 1/16 fixed-ratio converter with bidirectional capability can be operated as a boost converter with a K of 16/1.
Figure 2: BCMs with outputs connected in series for higher output voltage enable more design flexibility.
Figure 3: BCM converters are easy to parallel to meet higher power demands.
Additional design flexibility includes easy paralleling to meet higher power demands and the option of connecting converter outputs in series to boost output voltages by, in effect, changing the K factor.
Power delivery networks are undergoing significant changes due to the soaring power demands within many end markets and applications. EVs (electric vehicles), mild hybrid and plug-in hybrid vehicles are using higher PDN voltages such as 48V. The 48-V level meets the SELV (Safety Electrical Low Voltage) standard required by many systems, and the simple power equations of P = V×I and PLOSS = I2R explain why higher-voltage PDNs are more efficient.
For a given power level, the current is four times lower at 48V than in a 12-V system and has losses 16 times lower. At one-quarter of the current, the cables and connectors can be smaller, weigh less and be inexpensive. The 48-V battery used in hybrid vehicles has four times the power of a 12-V source, and the added power can be used in powertrain applications to reduce CO2 emissions, improve gas mileage, and handle new safety and entertainment features.
The addition of AI (artificial intelligence) in data centers has driven rack power dissipation above 20kW which has made the use of a 12-V PDN bulky and less efficient. Use of a 48-V PDN brings the same benefits here as with hybrid vehicles. In both automotive and data center applications, the preference is to keep 12-V legacy loads and PoL commodity buck regulators to minimize the amount of change.
Because 48V is SELV-compliant, a non-isolated fixed-ratio converter is a good choice for the 48-to-12V DC-DC conversion stage, as today’s PoL 12-V regulators can handle the variation in input voltage. A non-isolated, unregulated fixed-ratio converter is the most efficient high-power bus converter. It lowers power dissipation, boosts power density, and cuts costs. Its high density allows new decentralized distributed power architectures in hybrid automobiles where non‑isolated fixed-ratio converters can sit near the loads, making possible smaller and more efficient 48-V PDN wiring throughout the vehicle. In server blades, a small non‑isolated 48-to-12-V fixed-ratio converter can sit on the motherboard close to the buck regulators.
Many new AI accelerator cards, such as the SXM from Nvidia and the OAM cards from Open Compute Project (OCP) members, are designed with a 48-V input because the AI processors consume 500 – 750W. Cloud computing and server companies still using 12-V PDN backplanes in their racks require 12-to-48V conversion to employ these high‑performance cards. Equipping these accelerator cards with a bidirectional K = 1/4 non‑isolated fixed-ratio converter acting as a 12-to-48V boost converter (K = 4/1)—or within a distributed higher power 12-to-48V module—enables older rack systems to incorporate AI capability.
The world is now equipped with 4G radio and antenna towers which must be upgraded with new 5G systems consuming 5x the power of 4G equipment. The 4G PDN is 48V and is delivered via cable from a ground-based power system. The significant rise in power consumed by 5G equipment would force use of a large-diameter and heavy power cable were the PDN to stay at 48V. So telecommunications companies are currently looking at using a 380-VDC PDN to significantly reduce the cable size.
Use of a bidirectional K 1/8 fixed-ratio converter in boost mode lets the ground-based 48-V power system deliver 380V (K: 8/1) to the top of the tower. A 380-to-48V regulated converter at the top of the tower will allow both 5G and 4G systems to receive a regulated 48-V supply and realize less expensive power delivery via a small 380-V power cable.
Figure 4: Tethered drones are an example of a situation where power cables must be as light as possible. High-voltage converters can help reduce the size and weight of the tethering.
Tethered drones are another high-voltage application that requires isolation. Power cables for tethered drones can be over 400-m long, and the drone must lift this cable weight when flying. Use of a high voltage such as 800V helps reduce the size and weight of the tethering power cables. A compact onboard fixed-ratio converter, typically K = 1/16, can step power down to 48V for the onboard electronics and video payloads.
In EVs, high power demands make 400V a common choice for battery voltage. The 400V is then converted to 48V for distribution to the various loads around the powertrain and chassis. For fast-charging, the 400-V battery is charged from a charging station having a regulated 800-VDC output via an 800-to-400V converter.
Figure 5: A decentralized 48-V architecture places multiple smaller, lower-power converters closer to the 12-V loads.
In both the 400/48-V and 800/400-V applications, a parallel array of isolated K: 1/8 (400/48) and K: 1/2 (800/400) fixed-ratio converters with high power density and efficiency above 98% can work effectively. Regulation comes either before or after the fixed-ratio converter stage. The power density and efficiency gains of not having regulation also simplifies thermal management.
Exascale High Performance Computing (HPC) systems use 380VDC as the main PDN because rack power levels typically exceed 100kW. In these applications, isolated fixed‑ratio converters of K: 1/8 and K: 1/16 are integrated onto the server blades or on mezzanine cards distributed through the rack to deliver either 48V or 12V to the motherboards. Regulation then comes via a 12-V multi-phase buck converter array or advanced higher-efficiency 48-V-to-PoL architectures. The density and efficiency of the fixed-ratio converter again plays a critical role in enabling this type of PDN architecture to deliver high performance.
Figure 6: The Vicor NBM2317 enables efficient conversion from 48-to-12V and vice versa as it is a bidirectional converter. The bi-directionality enables integrating a legacy board into a 48-V infrastructure or the latest GPU into a legacy 12-V rack.
Advanced systems in enterprise and high-performance computing, communications and network infrastructure, autonomous vehicles and numerous transportation applications are just a few of the high-growth industries clamoring for more power. These applications have a common thread: Each has extreme power requirements and benefits from a small, power-dense DC-DC converter that can save space and weight. Power system engineers should consider fixed-ratio converters as an important and flexible way of enabling high-performing PDNs that provide a competitive advantage in overall system performance.
This article was originally published by Power Electronic Tips.
Mr. Davies has served as our Corporate Vice President, Global Sales and Marketing, since February 2011. Prior to joining the Corporation, Mr. Davies was employed by the Solid State Light Engine business unit of OSRAM Sylvania as Business Creation Team Leader from September 2010 to February 2011. Mr. Davies served in various positions with Analog Devices, Inc., a manufacturer of high-performance analog, mixed signal and digital signal processing integrated circuits, most recently as Director of World Wide Business Development. Mr. Davies received a B.S.E.E. and a Masters degree in Power Electronics from the University of Glamorgan.
Phil Davies, Corporate Vice President, Global Sales and Marketing
Build better UAVs using modular power
Power Delivery Networks (PDN) based on Vicor high performance power modules enable innovative designs for the next generation of UAV development
High-efficiency, high-density modules free up space for advanced communications and extend range
High-efficiency class of UAV depend on solar power to meet its long flight time requirements
High-density, high-power modules enable lighter, safer, lower cost tether cables to extend missions
This class of unmanned vehicle is powered and controlled via a tether from a ground-based power source assisting in extended missions
DCM DC-DC converters double the internal bus power and help keep the aircraft as light as possible
High-altitude long-endurance (HALE) UAVs are essentially flying satellites, designed to operate at extremely high altitudes for extended periods